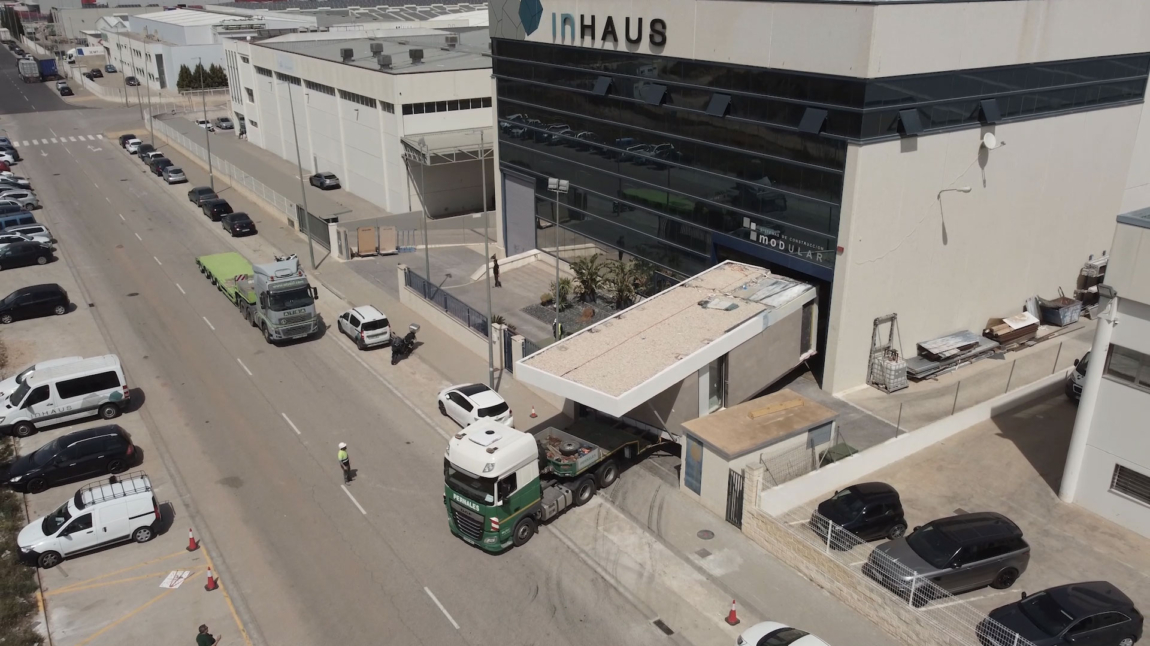
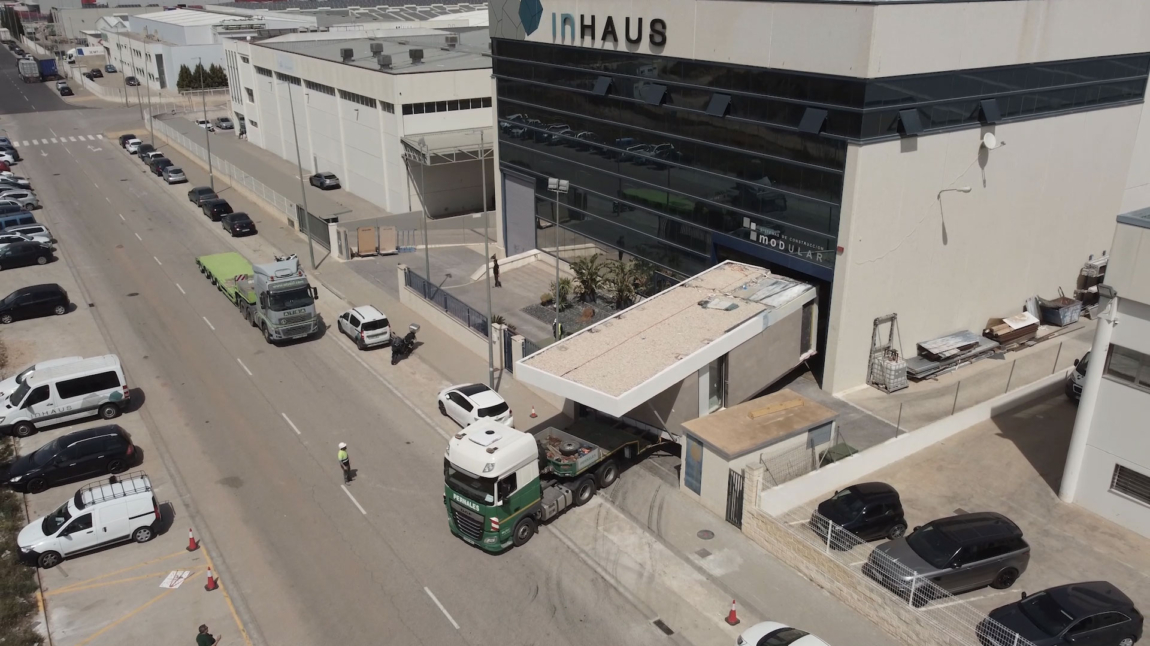
The industrialised construction of modular homes, a different and optimal way to build new homes compared to traditional construction processes. There is an increasing demand for this type of house with turnkey service and premium qualities, partly thanks to the flexibility in design and customisation that they offer, as well as guaranteeing the manufacture of houses quickly, efficiently and with closed costs. This type of construction refers to construction whose process or different parts of the process are carried out in a factory with industrial production methods, using innovative technology and specialised machines, to “produce” houses more productively and with standardised processes.
At inHAUS, industrialised building allows almost complete houses to be produced in series with standardised methods (not forgetting customisation) and the latest technologies. Industrialised construction is designed to be faster, more efficient and more sustainable than traditional construction.
Because of its rise, it is important to know and differentiate the terms that encompass these innovations, thus understanding how housing construction is being redefined. Below are several terms that are essential to understanding what industrialised construction is and which processes are best suited to your needs.
To begin with, it is necessary to differentiate between the three most commonly used terms in the sector: construction, manufacture and installation.
The term “implementation” refers to the exact moment when the prefabricated, modular house or its individual prefabricated components are transported to the site where the house is to be built, i.e. the plot of land chosen by the client to live on. During the implementation of the house, the factory-built elements are assembled on site and work is carried out on the completion and finishing of each house.
Manufacture of houses: when we refer to the development of a modular or prefabricated house project, the correct term to refer to its construction is “manufacture”, since the process of making the house is carried out in a factory, and then transported to the site. In this way, the houses are “produced” in a factory, with standardised methods and greater quality control..
There are various forms of housing construction or manufacturing
Component manufacturing is based on the creation of individual building elements in a controlled environment before assembly at the final site. This means that companies can component manufacture specific parts of the house, such as stairs or a dressing room, and then include them in a house. Component manufacturing therefore allows the creation of each individual housing element or part in a controlled manner in a factory, and then joining these components together.
Modular manufacturing: based mainly on the design and manufacture of independent units known as modules. These modules are manufactured in controlled facilities and then transported to the final site and all the joints are made to implement the house on the plot. The modules can coincide with rooms of the house such as bathrooms, kitchens, bedrooms… and are even covered with traditional building materials but adapted in weight and shape to be transported. Once they are finished in the factory, they are moved to the site and assembled there. Although the house is designed as a stand-alone unit, the level of precision is at the highest level and there is no visual difference to a traditional brick house.
At inHAUS, our modular construction allows us greater quality control and safety in the manufacture of the house, as well as the possibility of avoiding inconveniences derived from the climate or the terrain, as occurs in traditional construction.
Often confused with modular, but there is a key difference. Prefabricated building is not built in parts or modules, a complete house is created ready to be transported to the site. In this way, the house leaves the factory finished, but the materials used are lighter than in modular construction and the design is less flexible. There are also key advantages such as the reduction of site work and the avoidance of inconvenience, faster and more agile processes.
Offsite construction is another term that is currently prominent in the sector. It refers to any type of process, manufacturing or construction that is carried out outside the final construction site. Depending on the construction system of each company (by components, 2D, prefabricated construction…), a certain amount of offsite construction will be achieved. For example, at inHAUS, we manage to build 95% of our modular houses offsite, which means that only 5% of the process is carried out on the final site. This allows us to delocalise the construction of the houses and offers a significant advantage to the client, as they can see and control the construction of their house from our factory without having to travel to the site. Ideal for clients who are looking to build a second home away from their current location and cannot easily travel to the site.
Houses that are manufactured in controlled facilities from modules, then transported to the final plot and assembled on site. Once these houses are in place on the site, they cannot be moved. Since the joining of the modules, the necessary foundations, the urbanisation, finishes and final cladding are made for a particular terrain and orientation.
inHAUS modular homes allow flexibility in both exterior and interior design, as well as freedom of customisation according to the tastes and needs of each client. Finally, these homes have an aesthetic that has been carefully designed in detail with visual architectural elements such as overhangs, clean and geometric facades, porches and large windows. We have a catalogue of 111 luxury modular homes so that you can find inspiration or choose the model that best suits your tastes.
A type of housing that is manufactured in its entirety in a controlled manner on the company’s premises, creating the house already assembled in the factory. Once finished, it is transported compactly and completely to the site. These houses differ from modular houses in that they require the use of lighter materials as they are transported in their entirety, not in parts. In addition, they are not stable on the ground, they can be transported to any different terrain once they are already in place.
Modular and prefabricated building is revolutionising the way we think about housing. With benefits ranging from energy efficiency to reduced construction time, these technologies are setting a new standard in the construction industry. At inHAUS we are committed to conveying that there is a different and more efficient way to build than the traditional way, thanks to our 3D industrialised construction system. Our modular houses with turnkey service adapt to the personalisation of each client, with closed deadlines and prices.
Whether you are an individual or a professional, do not hesitate to contact us for further information to request a personalised quote or to make any enquiry.
In our Catalogue 111 you have more than a hundred models of houses to choose from. Register to access information and prices of all models.
"*" indicates required fields
Whether you are an individual or a professional, do not hesitate to contact us for further information, to request a personalised quote or to make any enquiry.
In our Catalogue 111 you have more than a hundred models of houses to choose from. Register to access information and prices of all models.